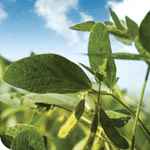
For a time the issue was a standoff: Does it take more energy to make ethanol than it provides?
One side argued it took more BTUs to make ethanol than it produced. Facing off against them were those who challenged how those BTUs should be calculated. Study after study came out in support of one side or the other. In the meantime, ethanol production improved. Today the process yields more energy and the entire supply chain requires less energy. The current stats have silenced many critics.
As one long-term supporter of ethanol explained, “In addition to simply over-counting the energy used in producing ethanol, detractors fail to recognize the significant gains of recent years in yields and energy used in processing. Modern ethanol plants are producing 15% more ethanol from a bushel of corn, and using 20% less energy to do so than just five years ago.”
Many advances have contributed to the efficiency of ethanol production. Thanks to improved farming practices, the US corn yield per acre has been increasing since 1975. Forty percent of the energy needed in raising corn comes from nitrogen. And nitrogen efficiency has increased immensely. The processing side of ethanol has become much more energy efficient as well. New enzyme technology has improved the ethanol process. Advances in heat recovery, the recovery and reuse of water that was previously disposed of as wastewater, and more efficient wastewater treatment systems have all resulted in a process that takes less energy. Recent calculations put the energy output to energy input ratio for converting irrigated corn to ethanol at 1.67 to 1. The fact that the ethanol energy balance is improving by the year has the potential to make us all winners.
Biodiesel production, on the other hand, has not been fraught with as much controversy. The production process of biodiesel and diesel is practically the same in terms of efficiency in the conversion of raw materials into fuel. However, biodiesel is able to use renewable resources in its production while conventional diesel requires fossil fuel resources. Biodiesel production yields 3.2 units of fuel product energy for every unit of fossil energy consumed in its life cycle. Another benefit of biodiesel is that for all the carbon emitted into the atmosphere from burning biodiesel, that same amount of carbon is taken out of the atmosphere by the soybean or other plant material.
SSOE is now introducing a proprietary process to save space and energy in the production of biodiesel. Because SSOE’s process does not water wash the biodiesel, it saves both the energy typically needed to dry the biodiesel and the space and cost of the dryer. Both ethanol and biodiesel production allow us to buy our energy here at home and lessens the transfer of US wealth overseas. Every effort toward efficient production of alternative fuels is a step toward energy independence.
SSOE has four new ethanol and four new biodiesel projects in progress.
Ethanol plants include:
- Vision Fuels in Boone, Iowa;
110 million gallons/year - Granite Falls Energy in Granite Falls, Minnesota; 50 million gallons/year expansion
- Glacial Lakes Energy in Vermillion, South Dakota; 55 million gallons/year
- Go Ethanol in Lima Ohio; 56 million gallons/year
Biodiesel plants include:
- Boot Heel in Caruthersville, Missouri;
30 million gallons/year - American Biodiesel in Toledo, Ohio;
30 million gallons/year - Three Rivers Biodiesel in Burnsville, Mississippi; 30 million gallons/year
- Freedom Fuels in Mason City, Iowa;
30 million gallons/year