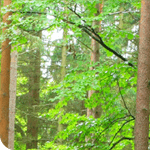
In the December ’06 Dimensions, we discussed methods and strategies for creating more eco-friendly manufacturing facilities and buildings by following LEED(TM) standards. And more recently, we discussed how to manage energy usage in the manufacturing process. In this issue, we look at reduction and recycling of waste associated with the product itself.
Many communities throughout the US have instituted a new annual Saturday event. It’s the day residents can bring electronic appliances and devices to a designated location for disposal. By the end of the day the site has separate mountains of TVs, dehumidifiers, computer monitors, telephones, printers and the like. It’s an unsettling picture that would be even more unsettling if we saw them actually being dumped into a landfill.
For the vast majority of people in developed countries, dealing with electronics waste at home or in their businesses is a hands-on experience. It has caused consumer groups and some governmental bodies to pressure manufacturers to take responsibility for minimizing waste through recycle and reuse. To varying degrees these grass-roots efforts are working. Many manufacturers are stepping up to the plate to address the problem in two ways. One is to manufacture their products so that they contain lower levels of toxic elements such as lead and mercury and a greater percentage can be recycled or reused. The other is to facilitate the collection and recycling process through “Product Takeback” programs.
The US has lagged behind other countries in actually requiring manufacturers to address product lifecycle issues. In Europe for example, the European Union made the “Waste Electrical and Electronic Equipment Directive” (WEEE) a law. It charges product manufacturers with the responsibility for recovering end-of-life electronics and disposing of them properly at their own expense. With prevention of waste being the foremost concern, the law encompasses not just manufacturers, but all those involved in the lifecycle of EEEs—producers, distributors and consumers. To ensure that recovery of the products takes place, the law mandates that manufacturers have an infrastructure for collecting electronics so that private households have a means of returning them to the manufacturer free of charge.
First Solar, one of the fastest growing manufacturers of thin film solar modules, is a model of sustainable product lifecycle practices. Their recycling program assures that essentially all components of the modules, including the glass and the encapsulated semiconductor materials and metals, are treated and processed for recycling into new modules or other products.
The process involves separating the layers of glass in the panel through a crushing process, cleaning the glass and providing it to glass manufacturers for recycling. They also separate the metal layers from the remaining module components into a filter cake and send the filter cake to a third party who will purify the metals so they can be recycled into commercial products. The results are that a significant majority of the module (by weight) is processed for recycling and thereby prevented from entering the waste stream.
Let’s take one step back in this process—collecting the modules back from the end user, typically large-scale solar power plants. Anyone possessing a module can request collection and recycling at any time at no cost. For each module sold, First Solar sets aside sufficient funds to meet the estimated costs to make this happen. First Solar will pay all packaging, transportation and recycling costs; the end-user’s only responsibility is to disassemble and package the modules.
It’s fitting that a company that produces solar panels is a model for waste reduction. So can we expect the same for the production of alternative fuels? The good news is the byproduct of biodiesel, glycerin, can be used to make soap and, with some additional processing, a variety of other products. The fact that there is a glut of glycerin on the market isn’t necessarily the bad news because the situation is inspiring everyone from basement scientists, to farmers, to university researchers to come up with various valuable uses for glycerin. Among them are: home heating fuel, feed stock and propylene glycol which can be used as nontoxic antifreeze for automobiles.
In the case of ethanol production, its byproducts are primarily used in feedstock for cattle. Agricultural scientists have also discovered that the byproduct of ethanol fermentation from corn stover (the plant part remaining in the field after harvesting corn) can increase the structural stability and organic matter content of highly eroded soil. And one Minnesota ethanol company is turning ethanol byproducts into high-energy protein lick-blocks for cattle.
With a continued global focus on sustainability, we can look forward to a time when all manufacturers will voluntarily plan—in the product development stage—how their products, or its byproducts, can be recycled or reused. In the meantime, consumers can use their buying power to support companies that champion planet-friendly practices and take serious steps toward greener lifestyles.