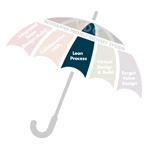
As we’ve discussed in previous posts, VDC is an umbrella for a number of concepts. One of these is the area of Lean Processes.
We recognize that to best serve our clients we must not only look to improve their systems, but our own as well. Ours is an industry that has not had the dramatic productivity improvements many other industries have seen in recent years. SSOE is committed to changing that. Lean processes aim to take the principles of Lean Production that many of our clients have pioneered in revolutionizing manufacturing and bring them, and their associated benefits, to the design / construction world.
Lean concepts, focused on eliminating waste and maximizing value, include:
Production planning (e.g. the Last Planner® System)
Production planning looks to smooth variations in design and construction work flow, develop planning foresight, and reduce uncertainty in project operations. Systems such as the Last Planner® System offer guidance and outline strategies such as:
- Planning in greater detail the closer you get to the work
- Developing the work plan in conjunction with those who are going to perform the work
- Identifying and removing work constraints ahead of time as a team to ensure work is ready for other design disciplines or construction trades
- Making reliable promises and driving work execution based on coordination and active negotiation with project participants
- Learning from plan failures by finding root causes and taking preventive actions
(source: Rethinking_Lookahead_Planning_to_Optimize_Construction_Workflow.pdf)
Improving work flow and productivity through work packaging
The concept of work packaging proposes that spending additional time to assemble manageable sized units of work results in improved productivity and a more successful outcome. This concept can be applied to both design and construction work. Frequently these packages are sized to be a week’s worth of work and are planned as the project progresses. The short and immediate time frame allows those packaging the work to lay out realistic expectations and ensure that all of the tasks in the plan for the upcoming week are constraint-free. Roadblocks are discovered and addressed (or planned around) while assembling the work packages, rather than stopping workers in their tracks and impeding progress.
Regular reflection and PDCA improvement cycle during the project
Plan, Do, Check, Act is a well-established continuous improvement tool at SSOE. While not exclusive to the VDC process, it is an instrumental tool to continuously ensuring model development is consistent with the needs of the project in order to avoid cycles of rework. It is also instrumental to proactively removing roadblocks to the flow of work to allow the effective work packaging described above.
Visual management with balanced, transparent metrics
Both VDC and Lean teach that plans and schedules should be in plain view for the entire team (including design, construction, and our client) with visual indicators that make it easy for everyone to quickly observe progress. This type of system:
- provides system alignment, goal clarity, engagement of people in the process, and improved communication and information sharing;
- simplifies and improves the means of delivery of information required to improve performance; helps people feel, see, hear, and touch mission, vision, core values, and results
- highlights critical information in ways that are difficult to ignore.
- keeps people focused on the real mission and goals of the organization.
- clarifies the core work of the organization.
- focuses attention on performance, and addresses performance issues at many levels.
- cuts through information overload so employees can see their results.
- makes the work more meaningful and fun!
Quality assurance
While technology offers an opportunity to improve quality, it cannot effectively address many human errors. To truly reduce the waste associated with errors technology is not enough. A systematic process is needed. This requires a shift away from just trying to catch errors through checking (although diligently performing design reviews at regular intervals is an important activity) and a move toward creating processes and check points that prevent errors. It also requires that when errors are detected, the focus should be on determining root causes and addressing the systems, conditions, or processes that caused them in order to prevent future errors.