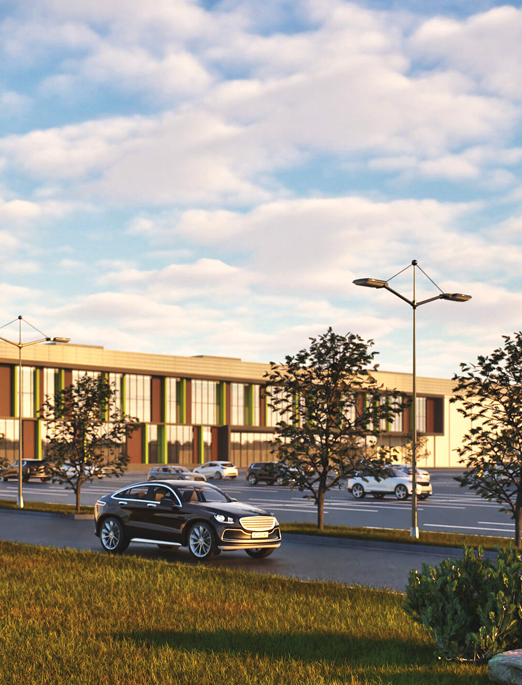
SSOE is providing design and engineering services for constructing a new greenfield solar cell manufacturing facility for a solar client. The project, once complete, will span approximately 1 million SF and will be designed to produce 5 GW of solar cell manufacturing per year.
Our team supported the client throughout the site selection and acquisition process, preparing a site due diligence report analyzing environmental, utility, zoning, site development, and permitting constraints. Our services also included master planning and early site development plans, including mass grading and stormwater management plans and specifications.
As part of the project, SSOE has worked closely with a Chinese Design Institute to assist in localizing the client’s technology used overseas to ensure compliance with all U.S. codes and standards. This involved extensive evaluation of the design basis, hazardous chemical usages and storage volumes, egress requirements, and modular construction methodologies. In this analysis, SSOE was able to optimize the facility layout to suit a uniform structural layout, fostering a modular concept for the cleanroom space of the production building.
Additionally, SSOE spent the early stages of the Schematic Design focusing on the most critical and highest value systems within the design. Through discrete analyses of the cleanroom classification, water purification, recycling, wastewater strategy, and process utilities, our team refined these concepts to provide more cost certainty to the client and the contracting community.
Our team also concentrated design efforts on critical path items, such as early earthwork packages, preliminary structural design including steel mill orders, and major facility equipment specifications to facilitate early procurement for long-lead items. As such, SSOE and the client have maintained the overall project schedule and the anticipated start of production timelines.
Construction on the project is expected to begin later this year with production beginning at the end of 2026.