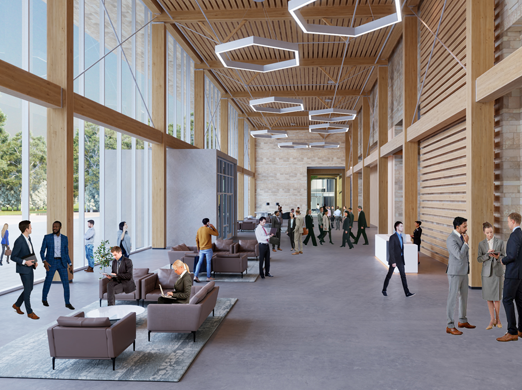
When a world-leading semiconductor manufacturer decided to build their largest-ever U.S. campus, they turned to SSOE as a trusted A&E partner to support making it a reality. The initial campus design and build-out includes two chip fabrication facilities (Fabs), a flagship office, entry building, parking, data centers, warehouses, chemical production and storage, and utility buildings. SSOE was invited to provide design support beginning with site planning, logistics, and enabling, continuing through full design and construction support.
SSOE has developed scope packages for select campus structures including:
- 52,000 SF flagship entry building. Serving as the public gateway to the facility and the aesthetic and brand-affirming focus for the campus, this space will host client and vendor VIPs, customers, and visitors. Featuring specialized mass-timber construction, it includes an auditorium and an employee wellness amenity center.
- 670,000 SF six-story high-rise office building. The nerve-center for the new campus, this building includes office spaces, labs, initial employee amenities, a café floor, campus operations and security centers, and a Fab cleanroom gowning space.
- 2,900 vehicle multi-story parking deck with an integrated 109,000 SF office building. This garage includes EV charging spaces, storage for campus vehicles, and a pedestrian bridge to the main office building for convenience. Additional employee offices are located above the top deck of the structure.
- Cleanroom-rated building link. Connecting the office structure with the factory floor, this structure allows employees to gown up and enter the cleanroom environment within the office building, and then move into the Fab while maximizing the square footage within the Fab for manufacturing activities.
- 100,000 SF warehouse with automated storage system and specialized systems for receipt of semiconductor fabrication tools and equipment.
- 15,000 SF independent data center to support the entire campus.
SSOE was also engaged to apply our modular and fabrication design expertise to executing specialty Lateral design with fabrication design services for both of the initial chip fabs.
A huge undertaking, really eight or nine large projects rolled into one program, our team has exceeded client expectations in terms of detail, thoroughness, and deliverables for every milestone. Our client partnership benefits from our steady contribution of creative design ideas to support not just the stated goals of this campus, but the client’s overall growth strategies.
The ongoing success of this project has resulted in SSOE being awarded design work for a sister facility.