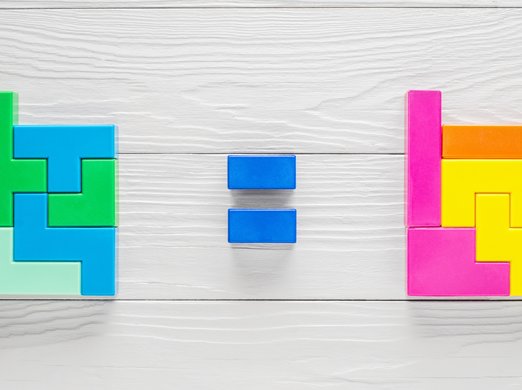
Integrated design of complex liquid and gas delivery systems broken into manageable pieces for repeatable off-site manufacturing and expedited design and construction.
Getting liquid and gas materials to and from semiconductor manufacturing tools is essential, and it involves a large amount of piping. SSOE is a go-to designer of subfab laterals for a leading semiconductor
manufacturer, and for good reason. When we were asked to provide lateral piping designs for twin semiconductor fabs, one in the Southwest U.S. and the other overseas on a tight timeline, we knew we had to change how we did things. On a typical project, SSOE would provide design documents which are transferred to a fabricator to develop the spool drawings for manufacturing. For these facilities, we modeled the piping to a fabrication-level of detail, and provided the fabrication drawings.
By embedding these details into the design, we put constructability at the forefront of the project and eliminated a series of RFI back-and-forth, thus providing the client with great savings to budget and schedule. We also delivered innovative time and cost savings by designing the pipe support racks and piping to be built off-site, transported to the site, and installed in large modular sections. And, in order to facilitate inventory tracking and installation of these units between off-site manufacturing and on-site installation, we developed an asset tracking system that is integrated within our design models. Using barcodes on each spool, we were able to track whether a particular module was in fabrication, storage, or already installed with up-to-the-minute accuracy.
We further multiplied the savings created by applying our industry and client-specific knowledge to identify “building block” modules which can be assembled in various configurations. By using these building blocks, our lateral designs could be adapted for new site locations with minimal adjustments, allowing us to effectively perform detailed design work for two facilities in parallel. And for projects where off-site manufacturing was feasible, like this one, we improved construction efficiency and safety by limiting on-site materials and minimizing the manpower and logistics needed to install the lateral racks and piping.