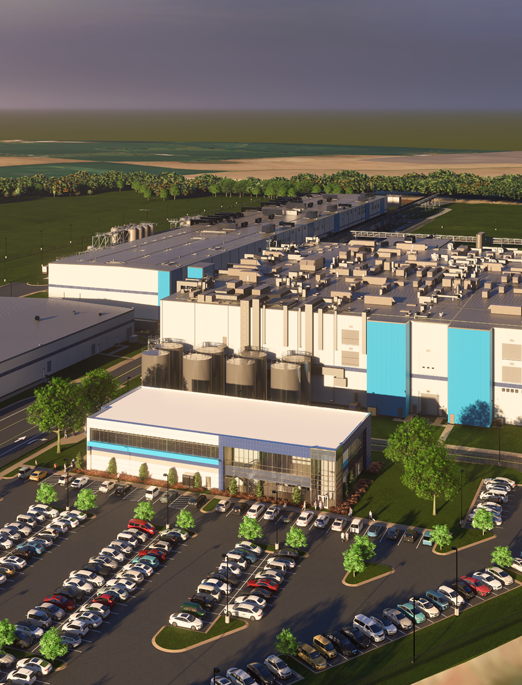
Ascend Elements, a leading provider of sustainable battery material solutions, began construction on its new EV battery recycling and engineered materials manufacturing facility. Known as Apex 1, this 140-acre campus in Hopkinsville will produce sustainable EV battery precursor (pCAM) and battery-ready cathode active materials (CAM) for up to 250,000 EVs annually.
SSOE initially conducted site and utility evaluations for Ascend Elements’ new flagship facility. SSOE supported the evaluation of potential sites for the new campus and provided a comprehensive evaluation that aided the client in selecting a site. During Front End Loading (FEL), SSOE developed a site layout to include process, packaging, warehousing, office buildings, a preliminary project schedule, and an execution plan. Our comprehensive team for this phase included architectural, civil, structural, process, mechanical (HVAC / plumbing), piping, electrical, instrumentation and controls, and estimating.
Throughout the design phase, SSOE worked with Ascend Elements and their process technology provider to create an efficient overall process design while exploring engineering alternatives to enhance project value. With Ascend Elements’ foreign OEM / technology provider, SSOE conducted evaluations of equipment and design specifications to ensure compliance with all U.S. codes and standards. This involved regular meetings and continuous BIM / CAD coordination.
SSOE collaborated with the Turner Construction Company / Kokosing Industrial joint venture to create the detailed design for this groundbreaking facility. Based on a design / build contract arrangement, the project benefited Ascend Elements by optimizing contractor-assisted design and Lean deliverables tailored precisely to the contractor’s requirements. This accelerated megasite project engaged 13 firms and more than 250 users across multiple countries. Lean leadership and real-time information reduced rework through a suite of tools, including Autodesk Construction Cloud, that virtually replicated co-location for an environment of collective efficiency.
This further enhanced the project’s success by streamlining information sharing across all parties, earning SSOE the Autodesk Design & Make AEC Best Construction Project Award in 2023. As a new player in the battery market, Ascend Elements trusted SSOE because of our established resources to deliver a project of this sheer magnitude, solidified by our agility in adapting to project execution throughout a dynamic, fast-track schedule.