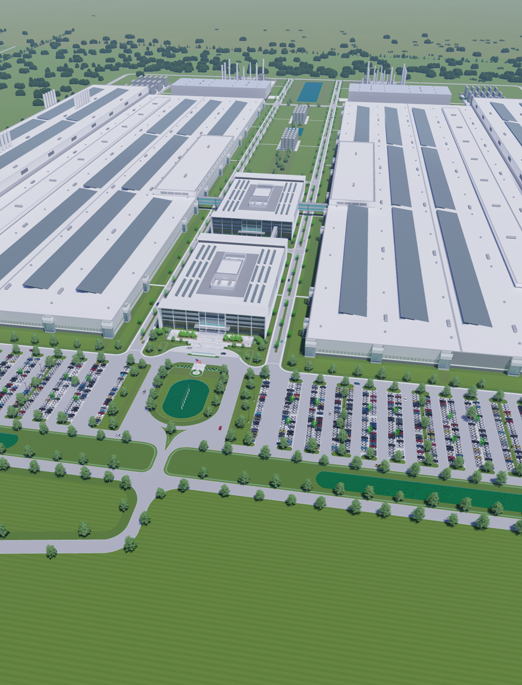
$100 million documented project savings to date with additional savings anticipated.
A well-known electric vehicle (EV) manufacturer has partnered with a leading non-domestic battery producer to develop an advanced battery chemistry aimed at enhancing EV performance. The goal of this collaboration is to offer customers improved battery value, durability, and fast-charging capabilities. To realize this vision, SSOE—a seasoned design firm with extensive experience in the EV and battery manufacturing sector—was selected to lead the engineering design and execution of the groundbreaking $1.5 billion investment.
SSOE partnered with construction firm Walbridge to implement a design / build delivery method. Since the project’s inception, all stakeholders worked closely to ensure unified project recommendations aligned with schedules and budgets. SSOE’s responsibilities encompassed the entire facility design, programming, and engineering.
The nearly 2 million SF facility includes production space and ancillary buildings supporting the main manufacturing area. Drawing on insights from the client’s existing battery manufacturing facilities, SSOE adapted their foreign manufacturing processes, building design, equipment, and layout to meet U.S. codes and standards throughout all design phases.
This greenfield battery plant marks the first U.S. location for the foreign client and will serve as their flagship facility in North America. Leveraging SSOE’s expertise in foreign direct investment, we’ve ensured a seamless transition for this global manufacturer as they establish operations in the U.S. Once operational, the plant is expected to add more than 18 GWh of battery capacity and employ over 2,500 workers, contributing to the local economy and advancing sustainable transportation.