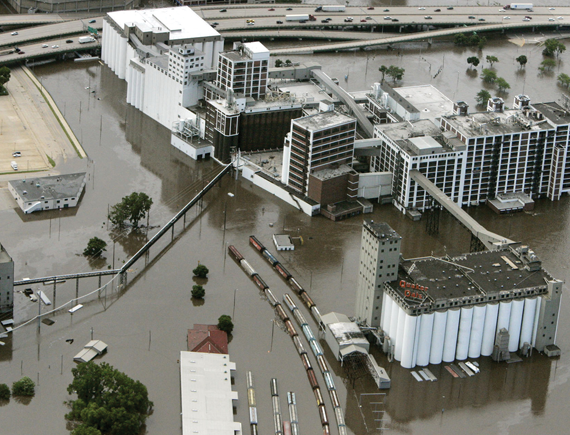
Expedited the recovery of process systems, helping the plant return to full operating capacity well within the client’s schedule.
In June 2008, widespread flooding submerged much of Iowa. This food client’s plant, one of the world’s largest food manufacturing facilities, was among the many businesses affected by the rising water. Located near a main river, the plant suffered considerable internal damage to operating equipment and was forced to stop production. Water filled the basement and rose nearly two feet into the first floor, destroying much of the on-hand product and damaging the facility’s operating process equipment.
The client called upon SSOE’s assistance to restore process operating systems as quickly as possible. Already familiar with the operation from previous projects, SSOE’s professional team initiated a comprehensive inventory of the process equipment in the flooded area and determined how to replace the damaged pieces. The team developed a master inventory list that prioritized tasks, documented vendor information, and tracked progress of rebuilding and purchasing of new equipment. The list was updated daily, keeping the entire team of contractors informed on required next steps.
Working with client’s staff and local contractors, SSOE also helped redesign and relocate the plant’s central compressed air system.
SSOE’s production process knowledge and dedication to our client’s success made our team a trusted advisor on this fast-track project. Just eight weeks following the flood, and well within the client’s established schedule, the facility returned to full operating capacity. In comparison, neighboring manufacturing plants were shutdown for several months while executing their recovery plans.