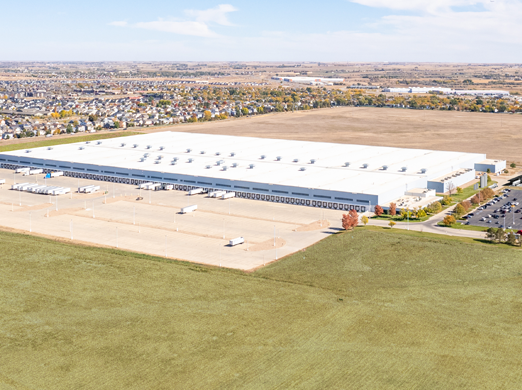
A pioneering battery manufacturer known for its high-density silicon-anode batteries is embarking on an ambitious expansion project. The company is converting a former Kmart distribution center into a state-of-the-art production plant. This move represents a significant leap from R&D to pilot manufacturing, to scaling up the production of their cutting-edge batteries used in phones, drones, military applications, and electric vertical takeoff and landing (EVTL) vehicles.
SSOE Group, with its recognized architectural and engineering design expertise in the battery manufacturing market, has partnered with Turner Construction to develop and construct the 775,000 SF facility, which is part of a more extensive 1.2 million SF multi-tenant complex. Phase 1 is engineered to have a production capacity of 500 megawatt-hours of battery power once in production.
Turner took the helm with site selection, evaluating potential sites across the U.S. Ultimately, a site in the west was selected offering an optimal climate, suitable humidity levels, and a robust utility infrastructure, complete with existing substations and the possibility for future expansions.
A rezoning effort was necessary to transition from a warehouse-only designation to one that includes manufacturing capabilities. SSOE and Turner provided expert support to a subsequent community engagement campaign, which was launched to dispel misconceptions and provide transparent information about the facility’s operations and processes. Despite facing initial resistance and a legal challenge
against the city, the rezoning efforts were successful, allowing the project to move forward.
Addressing the challenges presented by the brownfield site, SSOE’s team had to overcome layout limitations, which led to the design of an additional structure and modifications to the ceilings to create a suitable cleanroom environment. Moreover, relocating the process line from China to the U.S. required a detailed plan to comply with the diverse standards and regulations concerning electrical systems, utilities,
and piping, ensuring a seamless transition.
This company’s commitment to innovation and overcoming challenges, while harnessing the advantages of the environment and topography, position them to help transform the battery industry with its high-quality, dense power solutions.