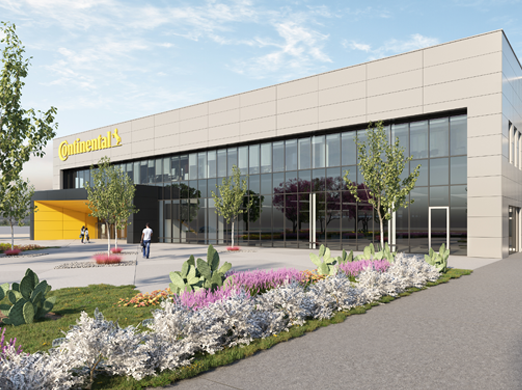
SSOE was selected by Continental AG to perform engineering, procurement, and construction management (EPCM) services for their new 215,000 SF state-of-the-art manufacturing facility located in New Braunfels, Texas. The plant manufactures products for Advanced Driver Assistance Systems (ADAS) that will help with assisted and automated driving. With ADAS in high demand by car manufacturers, this new facility positions Continental to expand its U.S. research and development footprint and manufacturing capabilities.
The new, future-oriented greenfield campus includes a production facility, office space, warehouse, guard shack, technical building, and cafeteria. The project also included campus infrastructure, integral roads, parking, truck docks, and other site requirements. The innovative, edgy design of the facility integrates with its environmental surroundings and fits the needs of a modern-world production environment.
A high priority for Continental, the facility was designed as a model for energy efficiency and sought LEED® Silver certification upon completion. To help the client meet this goal, SSOE capitalized on our extensive LEED certification experience and our vast network of LEED Accredited Professionals to help formulate a design strategy that fulfilled the client’s sustainability needs and expectations. This included an energy-efficient building shape and innovative solutions in building technologies. The project ultimately received LEED® Gold certification.
SSOE has extensive knowledge of Continental’s specifications and project execution preferences and has delivered successful facilities to them for over a decade. Our recent experience working together on Continental’s “Greenfield Plant of the Future” in Central Mexico was instrumental in leveraging lessons learned to drive efficiency into the facility design.