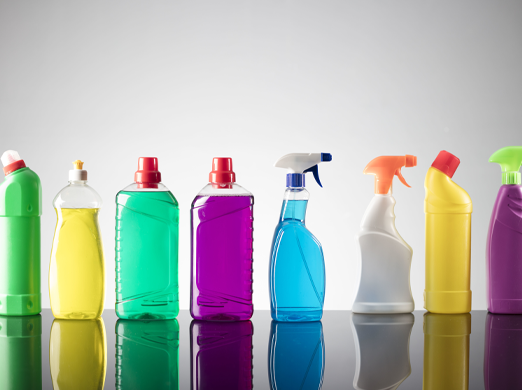
Through the design and implementation of a number of efficiency improvements such as equipment placement and repurposing to reduce process demands, SSOE was able to save the client $1.2 million in project costs.
Betco Corporation, a manufacturer of cleaning products, purchased a brownfield site in order to consolidate equipment and processes housed in three separate facilities into one central location. SSOE was selected to provide architectural and engineering services in support of the renovation and expansion efforts necessary to prepare the facility for operation. The expansion involved the renovation of 242,000 SF of manufacturing space and the addition of 54,640 SF to the facility.
SSOE drew from its extensive bench of engineers and architects to form an experienced team to work closely with Betco throughout the project. The team met with the client’s staff on a weekly basis to communicate progress and discuss any issues that may have arisen during the previous week. SSOE also assigned a chemical process engineer to work in the existing Betco facilities and assist in the evaluation and classification of the chemicals used in manufacturing their products.
Working together with Betco’s staff, the SSOE team completed front-end loading (FEL) for the project. During the FEL process, a conceptual layout of the site was developed, along with a 30% cost estimate and milestone schedule. As is the case with many small businesses, Betco did not have the internal staff to create P&IDs for the new operations, which led to SSOE creating a complete set of P&IDs for the new facility. In order to maintain operations in the existing facilities, a blend of new and existing equipment was included in the final layouts. Several processes were also analyzed and updated to significantly increase efficiency.
The code evaluation for this facility proved to be very complex. SSOE provided support in preliminary meetings with the county plans examiner and throughout the building permitting process. Fire walls were incorporated in the design to provide separation, with steel fireproofing for added protection and explosion relief. To effectively accommodate the large amounts of hazardous materials on-site, two additions were designed to isolate them from each other and the rest of the facility. This design was based on SSOE’s site evaluation and included minimizing piping lengths, considering truck deliveries, and minimizing the impact to existing utilities.